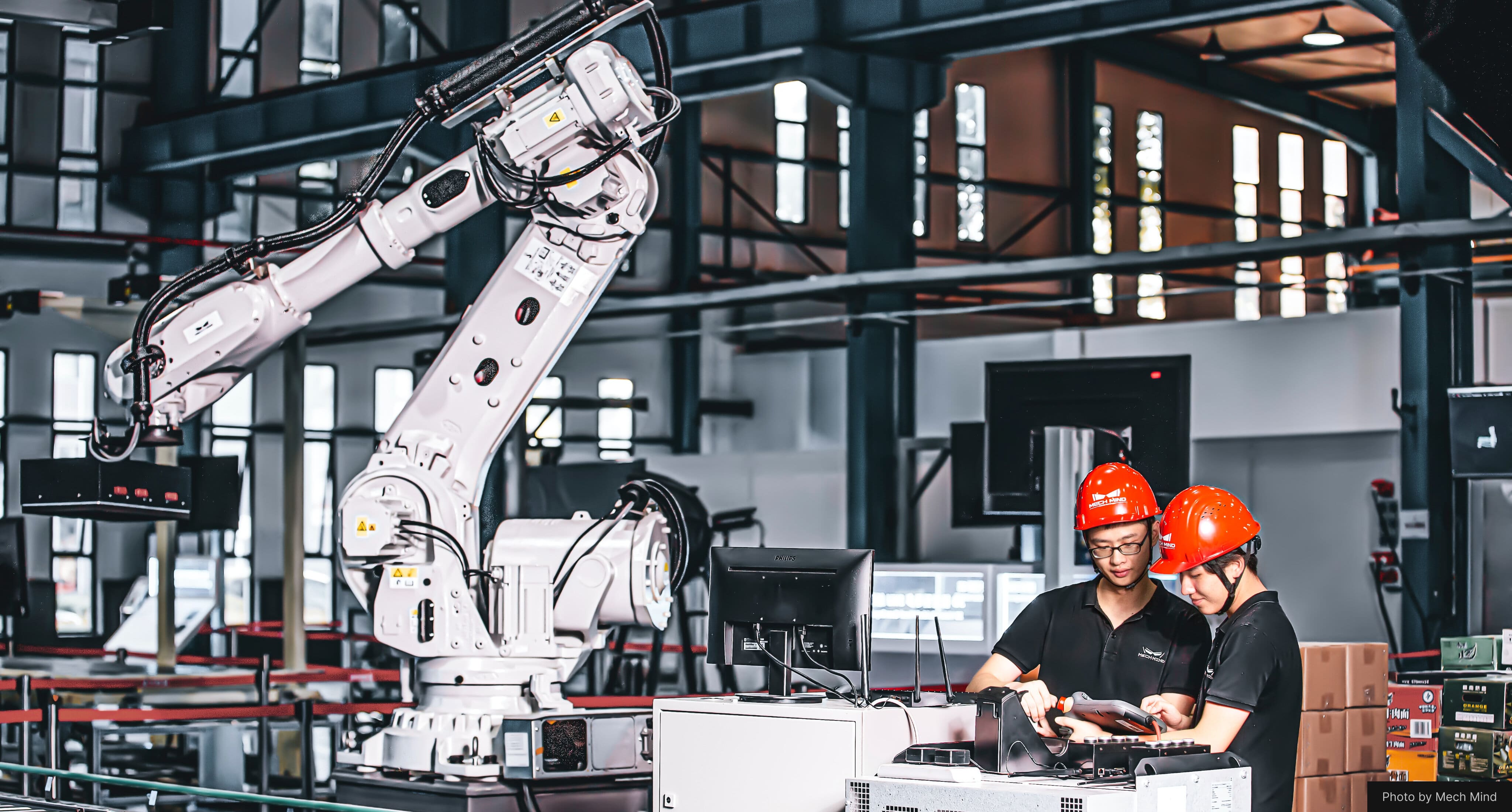
Why No-Code is the Solution for Manufacturers to Move to Industry 4.0
Industry 4.0 is a buzz word that pretty much everybody is talking about these days, but how and where do you get started? Manufacturing is considered one of the most complex industries, way more complex than most people would initially think. You're dealing with high-tech machines needed to do the heavy lifting and people that need to know how to operate those machines, so how do you connect those with the rest of the operation when you also have to run a sales and marketing organization to sell and market your products?
A rigid ERP as the core backbone
With the introduction of ERP in the early 90s many manufacturing organizations have grown into two distant operations: the shop floor vs. the office
Since most ERP's are often finance driven systems and deployed as desktop software (most desk workers don't need mobile access), other departments such as quality control, production monitoring, and maintenance are often neglected when it comes to ERP software. And so when each department starts using their own systems to manage their operations you get a bunch of islands with their own data silos. This prevents departments from sharing information easily and this can lead to massive inefficiencies between the shop floor, supply chain, and sales. Luckily, with Industry 4.0 and the advancement of software technology and common data protocols most organizations now start to see it's time for change.
But how do you get out of a jungle consisting of paper docs, excel sheets and rigid software systems?
If you ask any process engineer about the challenges they face on the shop floor, they’ll have no problem listing areas for improvement. However, manufacturers face significant problems hiring enough enough developers to build the applications they need to connect data silos and speed up innovation. And not only is there a shortage of developers, it can also easily get very expensive if you build applications from scratch with traditional programming.
And who knows a factory’s processes better than those tasked with improving them? This is the idea behind the no-code revolution. Over the past years, visual application development platforms have helped workers to create solutions to the challenges they face without technical skills. No-code platforms solve the problem by letting so called citizen developers and those on the factory floor build their own apps. And they also make it easier and much faster for dedicated IT staff to integrate and deploy them.
Over the past years, visual application development platforms have helped workers to create solutions to the challenges they face without technical skills.
Why no-code has the potential to change how manufacturers solve problems more than any other industry
Smart manufacturers are increasingly using no-code platforms to get rid of paper processes and manual data entry that power their digital transformation. But why do we think that no-code platforms have the potential to be more disruptive in manufacturing than other industries?
Well, when you sum up the main benefits of no-code it shouldn't come as a surprise that:
1. You can build applications about 10x faster than traditional programming
2. Everybody can learn to build an app in a day (no learning curve and you don't need technical skills)
3. It's easy to iterate and make changes (even co-workers can make changes to apps they didn't build themselves)
4. The costs are much lower (even though you pay a license fee for the software, your savings vs. traditional development are significant)
Hopefully this helps to outline exactly why manufacturing needs no code. However, there's another reason why we think that no-code can be disruptive to manufacturing and this all comes back to our first point:
Existing ERP and MES systems are often very inflexible and they aren't connected to the rest of the operation
If there’s one word to describe traditional manufacturing software, it’s “rigid.” Many ERP systems aren't build to make quick changes, add new functionality or work with new technologies such as mobile apps, IoT, artificial intelligence, computer vision or optical character recognition (OCR). However, the fact that most ERP's are rigid isn't bad per se, it's often for a reason because ERP systems are at the core of most organizations and even a small unvalidated change can be desastrous.
This is why most manufacturers still work with paper and Excel, it's cheap and easy to work with. But it also has it's drawbacks:
1. A lack of real time data to drive important business decisions
2. No easy tracking and forecasting analysis on quality, production and maintenance KPIs
3. A lot of extra time spend on archiving and reporting
4. Paper documents aren't intuitive, you can't just pull up an instruction video or send a message for help
And yet, this is the biggest problem in manufacturing: since most production processes are so complex and specific, it's tough to go paperless if the underlying software is too rigid to make changes easily. This is why paper still dominates the shop floor, but with no-code this is all about to change.
Today, a lot of manufacturers produce customized products, there's no one-size-fits all anymore and production lines need to accommodate endless variations upon modular products. And with shorter product life cycles, thinner margins and just-in-time supply chains there's no room for mistakes.
And yet, this is the biggest problem in manufacturing: since production processes are very complex and specific, it's tough to go paperless if the underlying software is too rigid to make changes easily. This is why paper still dominates the shop floor, but with no-code this is all about to change.
With the latest advancements in no-code technology, you can now easily build complex apps that replace paper and Excel so you can innovate faster and get the data you need to drive important business decisions. And according to a recent survey by IQMS: “CIOs and their teams who are the most adept at integrating analytics, Business Intelligence (BI), real-time monitoring, and quality management are growing on average 10% faster than their peers.”
It's clear that no-code is here to stay and there are many reasons that manufacturers can benefit from no-code as well. There aren’t enough software engineers to meet demand. Product cycles are moving faster, margins are thinners, and there’s a greater need than ever for customized business apps on the shop floor. However, it’s important to remember that low-code is not the same as no-code. No-code is for process engineers, business analysts, lean experts and IT specialists. Low-code is for developers and involves coding. Although low-code is often better suited to build core ERP systems from scratch, low-code still is very complex whereas no-code is not.
Any2Info is the only all-in-one no-cloud platform that is changing the way apps are built in the industrial domain. Using Any2Info, process engineers and business analysts can create their own custom applications to collect data from people, machines and ERP systems to digitally transform the shop floor and gain real-time visibility of production processes within just a few days.